 |
 |
 |
 |
 |
 |
 |
 |
 |
 |
 |
 |
 |
 |
 |
 |
|
|
|
|
|
|
|
|
|
|
|
|
|
|
|
|
|
|
|
|
|
|
|
|
|
 |
|
|
|
|
|
|
|
|
|
|
|
|
|
|
|
|
|
|
|
|
|
Indexing Rotary | Lathe Axis
|
|
|
|
|
|
|
|
|
|
 |
|
|
|
|
|
|
Plasma Cutting Wood carving Aluminum machining
Wood turning Aluminum Turning
Project with Ben Cabrera of BenT Studio in Melbourne, FL.
Ben picked up a Delta Iron Bed wood lathe with a variable speed belt drive for about $200. This we aligned with the CNC gantry & bolted it to the bed cross rails.
The limiting factor I still think is the belt drives which I think get some tooth deflection and sometimes vibrates when the wood grain gets wonky.
They turned out pretty well all in all.
These were about 140 or so Sapele (mahogany family) spindles for a rail Ben was doing.
You can see the rotary axis behind, to the right that I swapped the stepper for an a/c induction motor to make it into a lathe axis.
The small 1/2hp 1725rpm motor from my old cement mixer shown below roasted once I put the 4" 4 jaw chuck in the 8" 3 jaw chuck. It turned the whole spindle--about 18min. But is was smoking afterwards. The motor was just too small for the mass is was spinning.
I had to get a 2hp, 1725rpm new & bore out the 2" pulley I had to fit the 7/8" shaft.
|
|
|
|
|
|
|
|
|
|
|
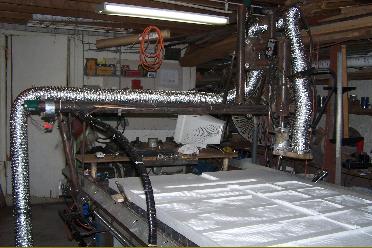 |
|
|
|
|
|
|
|
|
|
|
|
The 2hp motor draws 17.8 amps at 120V & if I want to be able to have the G-Code turn it off, I had to wire it into my relays & I only have 2 20 amp relays available & one was switching the dust collector, the other was only being used as a signal switch to turn on the router spindle. I was able to switch the router spindle to a lower amp relay & wire the new lathe motor to the secondary 20amp relay. I did make an external relay card using a salvaged 30 amp, 120V relay from some electronic board I had, but I put the 1/2" drill bit into the side of that relay & had to use a 16A 250V relay but that one was being controlled by a logic circuit that sent 12V out of the relay card so I could use it to trip the external relay. The problem was that there was some sort of interference with either the logic circuit or with the 12v circuit sending interference to the VFD router spindle and the C axis step & direction signal. So I had to abandon the idea of being able to run the lathe in reverse direction.
Below is the QuadRelay card where the lathe and the router motors are controlled.
|
|
|
|
|
|
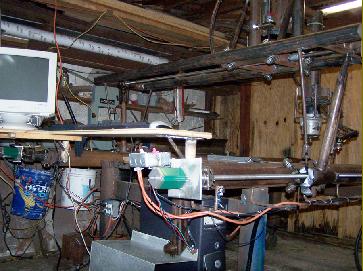 |
|
|
|
|
|
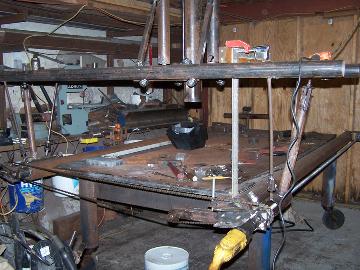 |
|
|
|
|
|
|
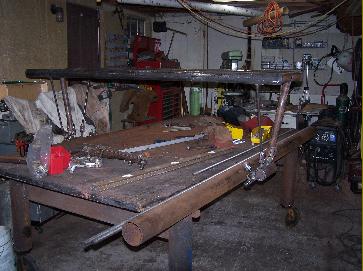 |
|
|
|
|
|
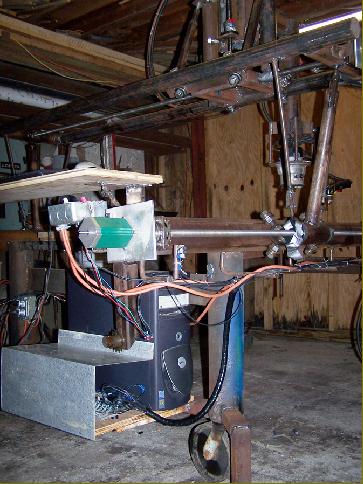 |
|
|
|
|
|
|
|
|
|
|
Another challenge was the bearings at the front face of the chuch shaft. The setup was initially for an indexing axis for plasma cutting pipe & tube, and the top bearing on the opposite face of the front plate was not perfectly in contact with the machined groove in the 2.5" sch40 pipe that is the axis shaft. While turning as a lathe, the cutting tool can cause the shaft to lift slightly and cause it to bounce/vibrate a little. The solution was to make a sort of lock-bearing on a steel plate that can be pressed down to the face of the shaft and locked in place with a lock bolt. The center bolt is the pivot point and the bearing can be levered to tight tolerance by prying up on the end of the bearing lock plate as the lock bolt is tightened.
|
|
|
|
|
|
|
|
|
|
|
|
|
|
The motor to the right is probably 50 yrs old or so, I think it may be a Baldor, but sure the HP, but it's a 3600rpm motor and is way too fast. I cannot gear it way down without getting really crazy with pulleys. So, the logical, & I believe most cost effective solution was to get the 2hp, 1725rpm motor. The new one is an AC induction motor with both a start & run capacitor.
|
|
|
|
|
|
|
|
|
|
|
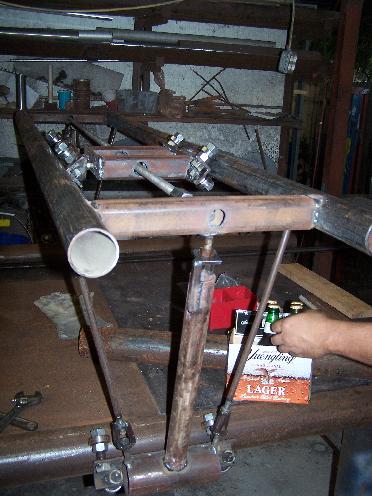 |
|
|
|
|
|
|
|
|
|
|
|
I think the speed is a little slow at about 975rpm. The pipe axis is 2.875" dia and the pulley is about 1.625" dia at the belt ID. I have a 2.5" OD pulley that we can machine to go onto the 7/8" motor shaft & that would get us about 1320 rpm which may give us a bit better finish.
|
|
|
|
|
|
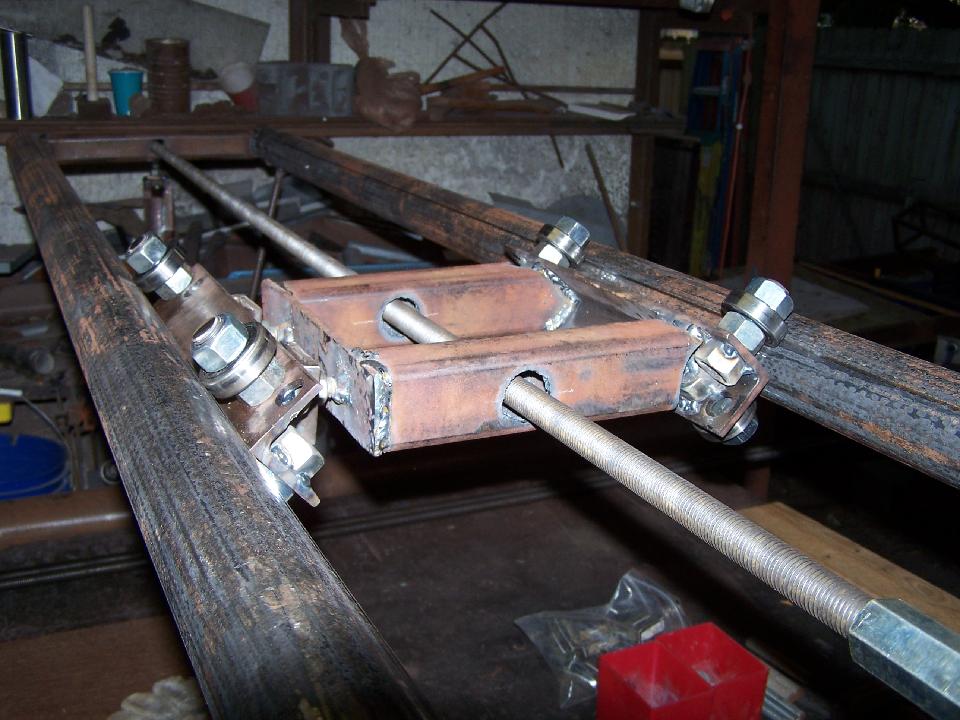 |
|
|
|
|
|
|
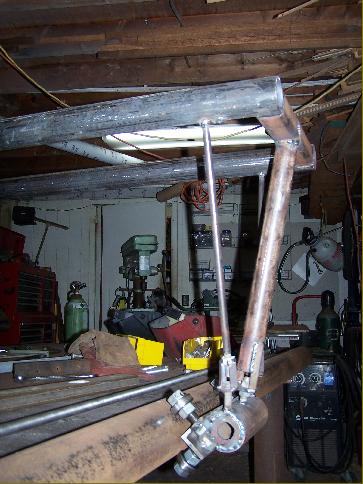 |
|
|
|
|